Case Studies
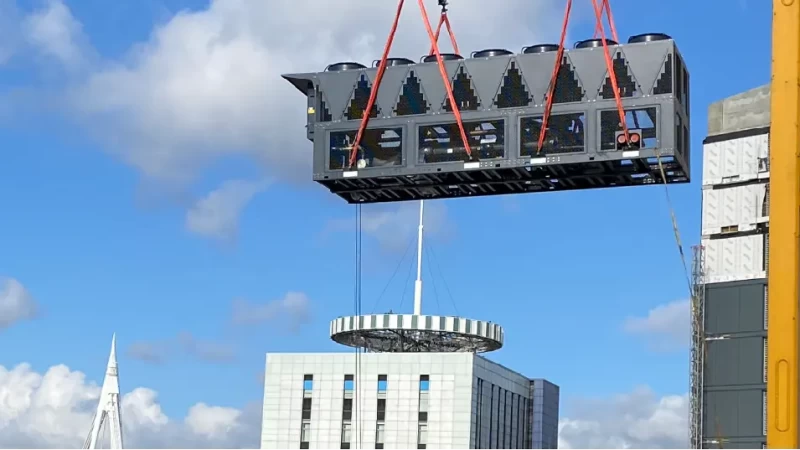
Cooltherm provide another cooling solution to the Cardiff Central Square group of projects
Chillers required for a 500,000 sq. ft building and development which included a 14-bay bus station and a 12-storey office spaces with a very specific footprint.
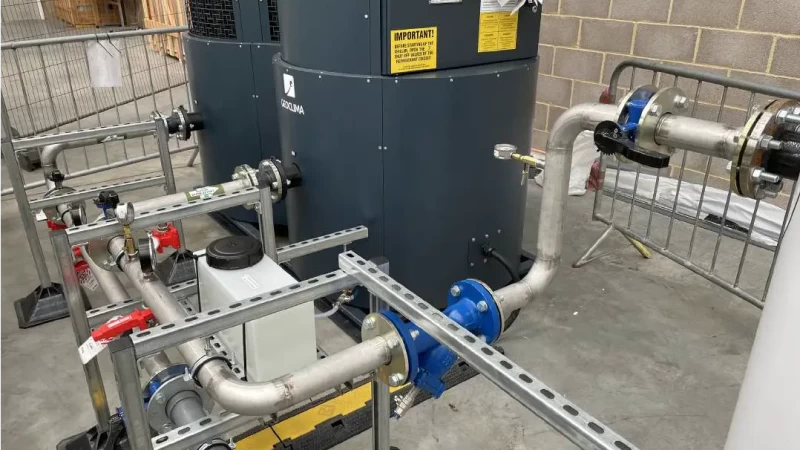
Innovative Circlemod Chillers Used to Meet Specification for the Subsea Pipe Industry
Located on the south coast of the United Kingdom, our customer required advanced cooling options for their process machinery and air handling unit.
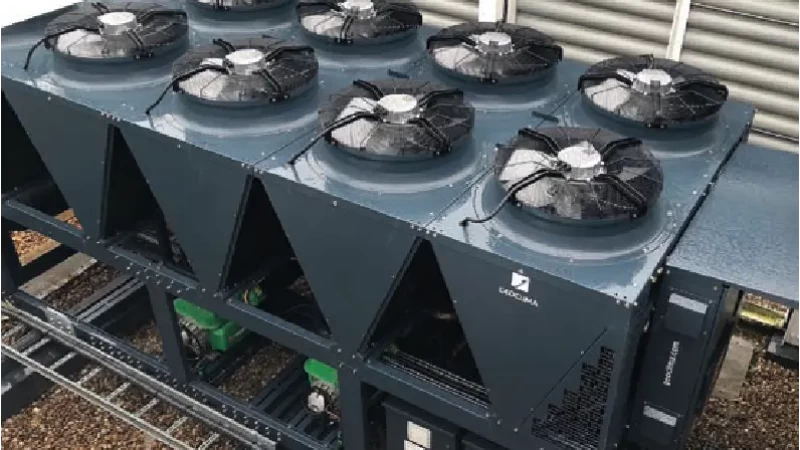
Chiller Installation for University of Bath Sports Village
Cooltherm was tasked with designing a chiller capable of delivering a total capacity of 450kW at the £35 million Sports Training Village at the University of Bath, which provides facilities to accommodate over 50 sports as well as being a world class multi-discipline training environment, and regularly hosts major international competitions.
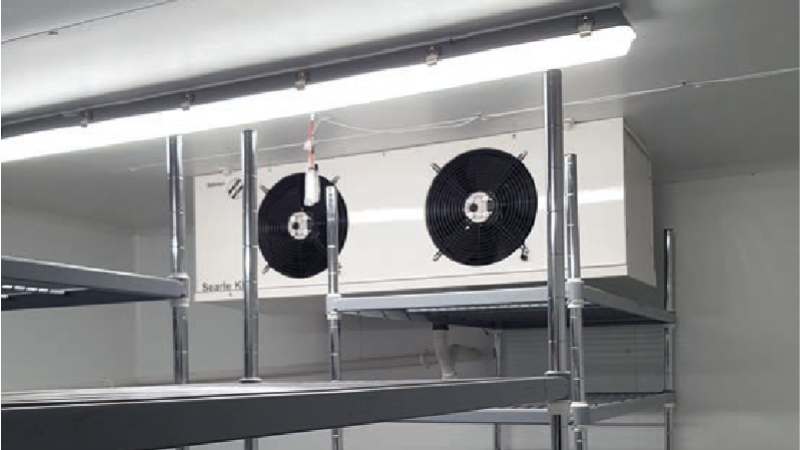
Bespoke Chiller Install at Royal Glamorgan Hospital
Specialist chiller and air conditioning design and installation business Cooltherm was chosen to design and install replacement chillers for the pharmacy cold room in the Royal Glamorgan Hospital, a district general hospital in South Wales.
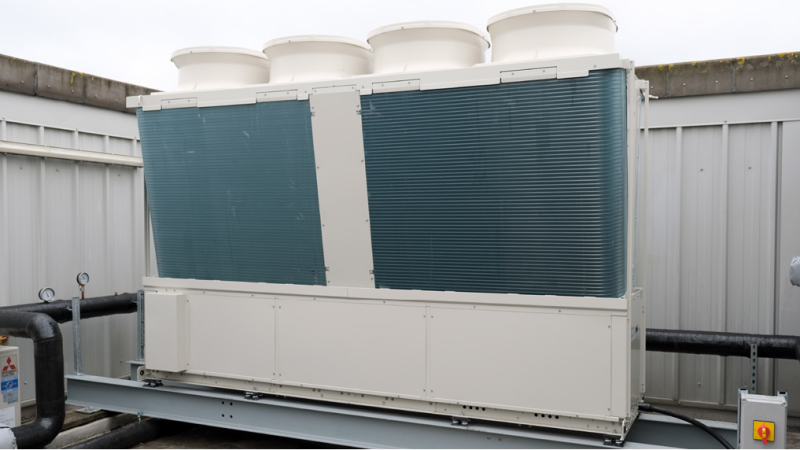
First large 180kW chiller installed in the UK
The specification for the replacement chiller was clear, it had to offer unparalleled levels of energy efficiency and be available ‘off the shelf’ with the installation needing to be completed within a few weeks.

Over £100,000 saved – Vodafone Testing Facility, Newbury
Alongside our longstanding partner Geoclima, Cooltherm worked on the replacement of existing HVAC equipment without impacting the client's operations.
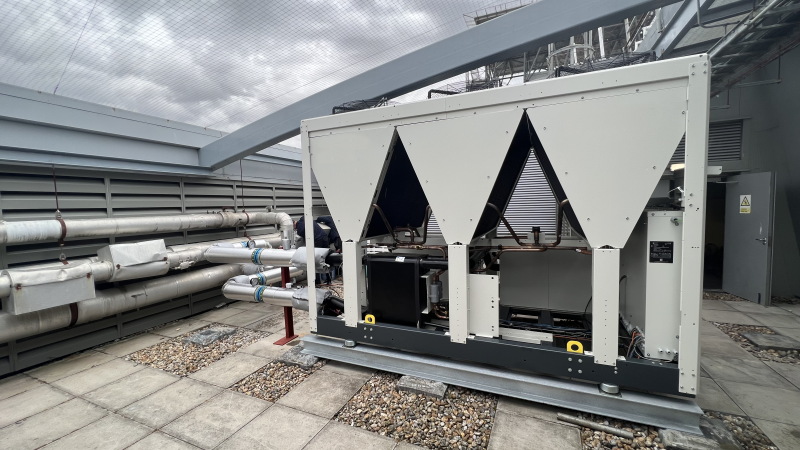
Chiller Replacement at Royal Alexandra Children's Hospital
Three chillers at the Royal Alexandra Children's Hospital needed to be replaced with low GWP alternatives. There was a key obstacle given the equipment's location that only Cooltherm had the capability to overcome. Read about what we achieved here.
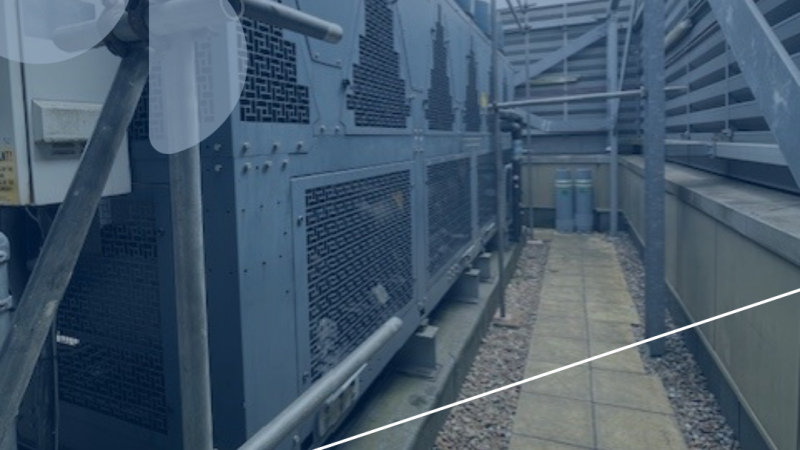
Keeping Cool Heads – Chiller Maintenance and Coil Replacement at Cardiff University
An issue with one of the University of Cardiff CUBRIC Building's chillers was spotted during a routine maintenance visit. Within 5 days, the issue was fixed and the chiller set up to prevent a reccurence in the future.