News
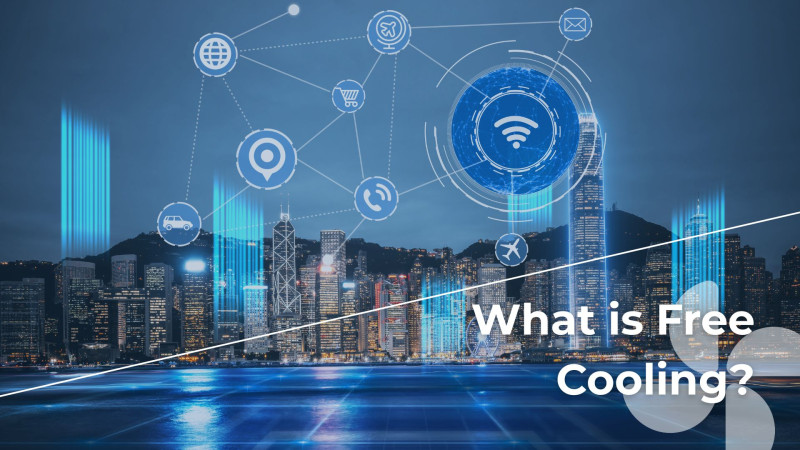
What Is Free Cooling?
Free cooling chillers offer a highly efficient method for reducing energy consumption, harnessing the naturally cool temperatures found in the ambient...
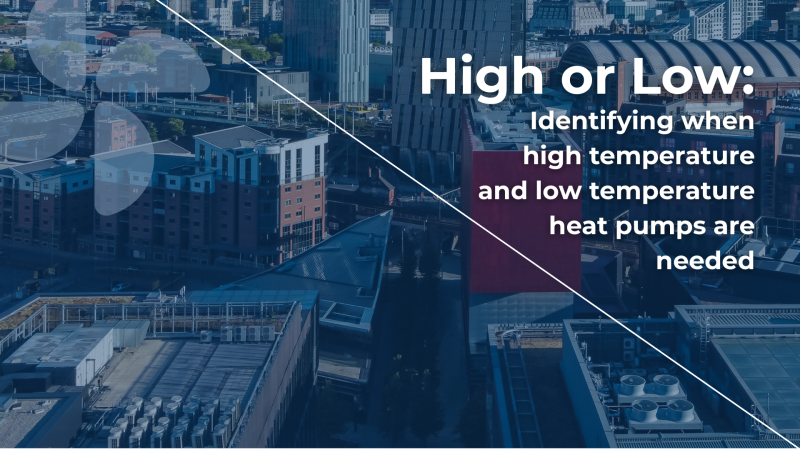
Heat Pumps: High vs Low – and when to choose which
With the transition to electric heating continuing with pace, heat pumps are an essential part of decarbonisation strategies for both new-builds and r...
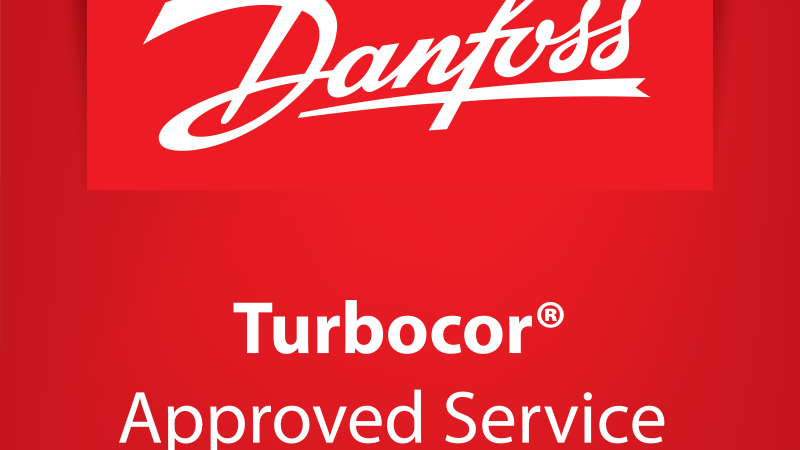
Cooltherm Recognised as Danfoss Turbocor® Approved Service Provider
Cooltherm is proud to announce its official accreditation as a Danfoss Turbocor® Approved Service Provider (TASP) – a significant milestone...
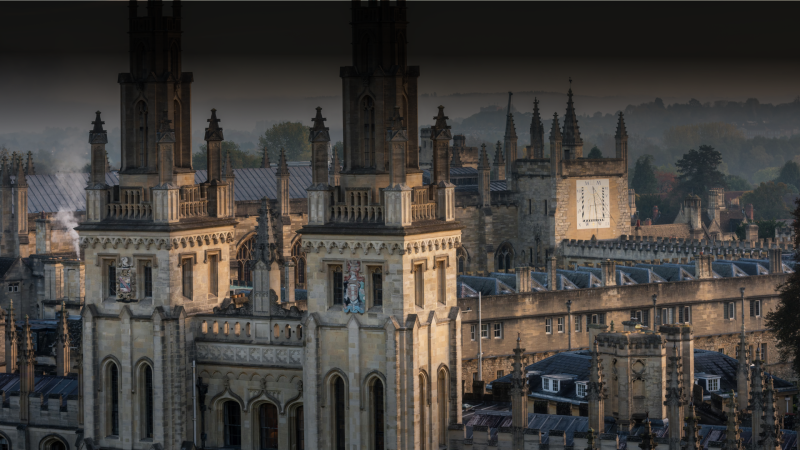
Decarbonising Heating in Historic Education Buildings with Heat Pumps
The UK’s education sector is home to many historic institutions, with buildings that have stood for over a century. While these structures boast...
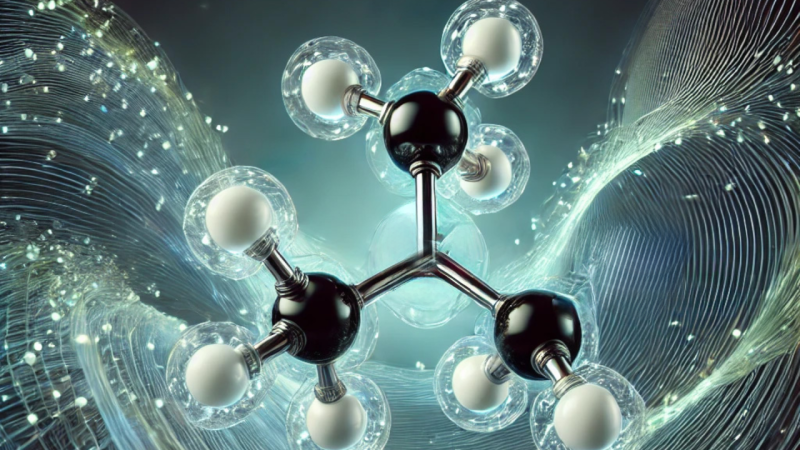
What is R290 (Propane)?
R290 is a natural refrigerant that has been gaining significant attention within the commercial heat pump sector.
As regulatory bodies tighten restri...
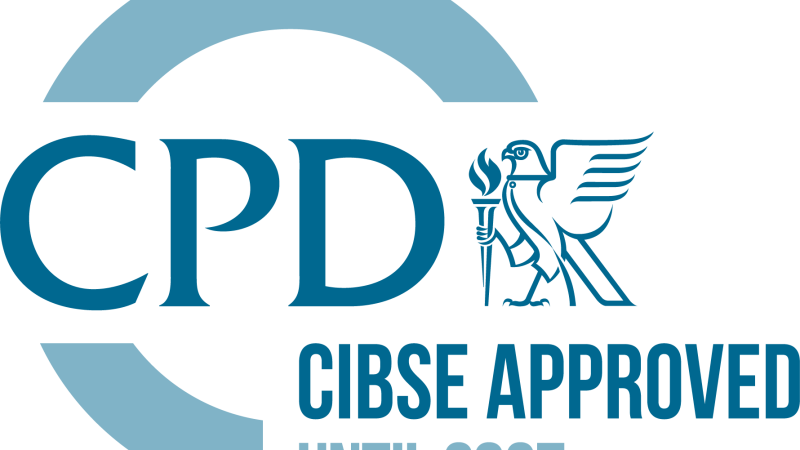
Navigating Refrigerant Legislation and Restrictions: Cooltherm’s Latest CPD Now Available
The HVAC industry is entering a phase of greater restriction in response to environmental pressures with new refrigerant regulations shaping the futur...
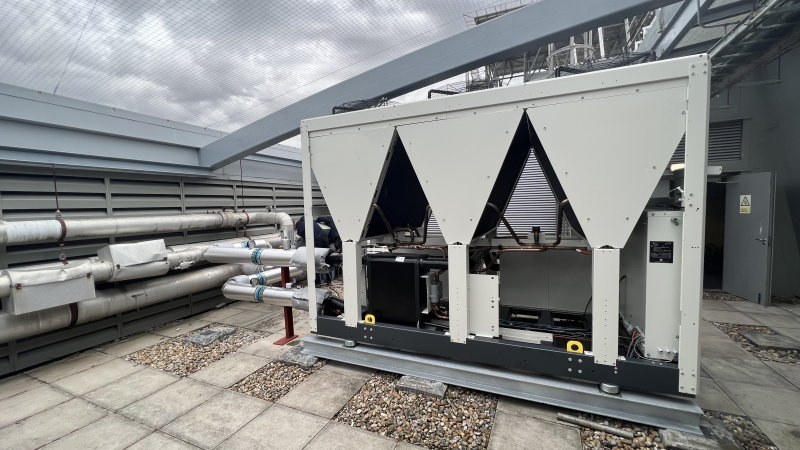
Climate Control in Healthcare: Key Factors to Consider
The healthcare sector presents a unique set of challenges and requirements when it comes to HVAC (heating, ventilation, and air conditioning) solution...
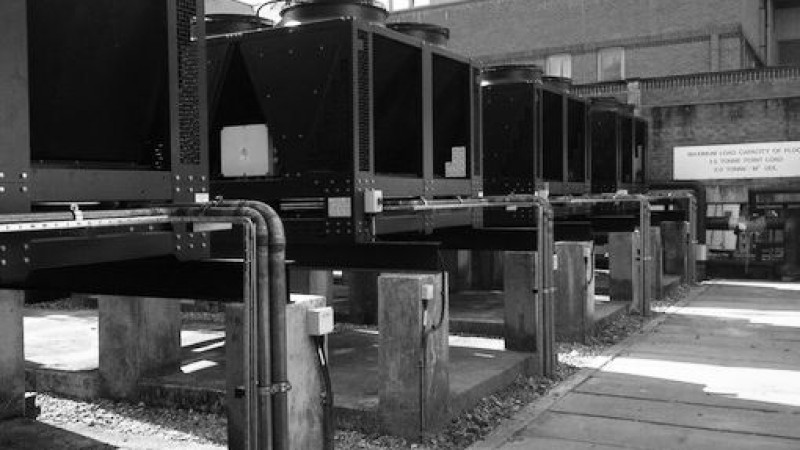
What is Coefficient of Performance (COP)?
The coefficient of performance (COP) is a crucial metric that measures the efficiency of a heat pump. It reflects the amount of heat a heat pump can g...
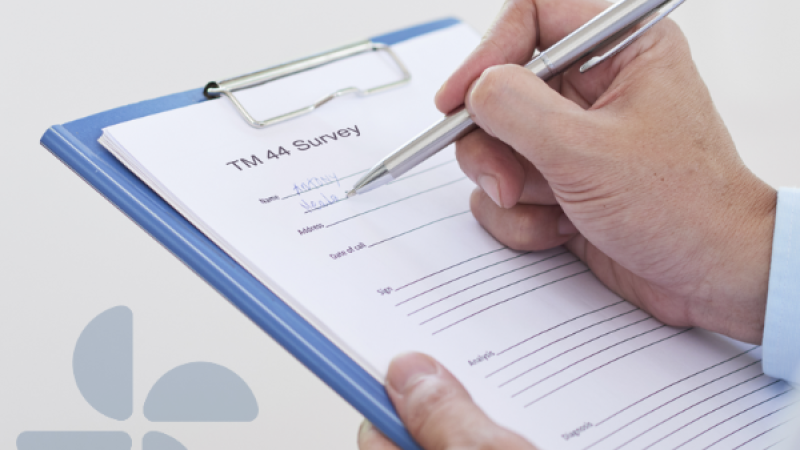
Why Do I Need a TM44 Survey?
For organisations that deploy air conditioning systems on their premises, understanding the role of TM44 survey is key to maintaining both compliance...
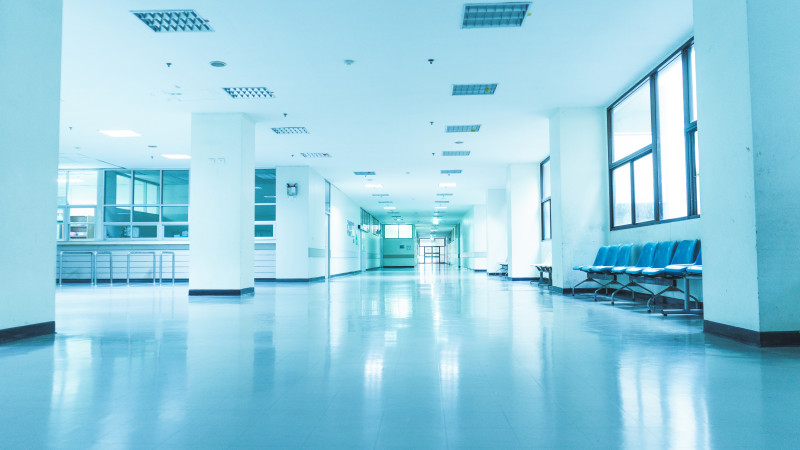
Healthcare Sector Grant Funding Available
As healthcare facilities across the UK face growing pressure to reduce their carbon footprint, Phase 4 of the UK Government’s Public Sector Deca...
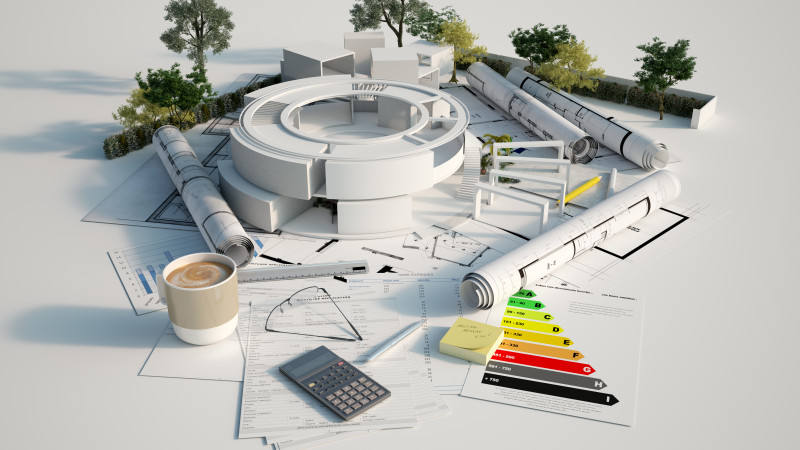
Unlock Decarbonisation Funding with Cooltherm’s Heat Pump Solutions
As Phase 4 of the UK Government’s Public Sector Decarbonisation Scheme (PSDS) launched on 23rd September 2024, public sector industries (includi...
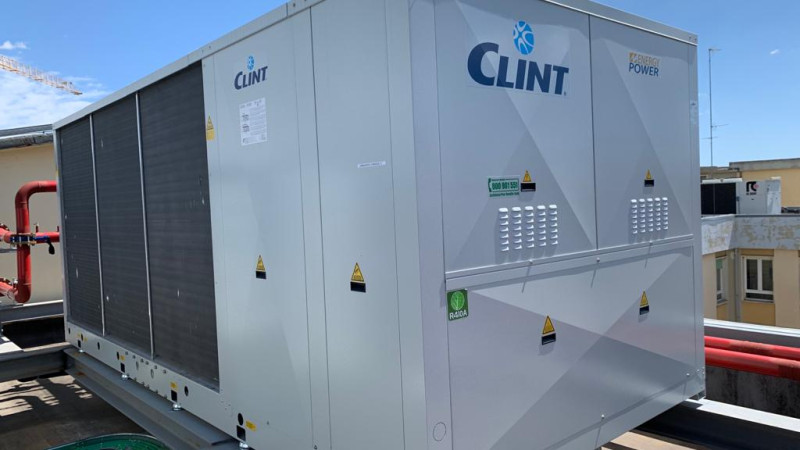
Cooltherm Enhances Market Presence
Cooltherm are excited to announce a new distribution agreement with Clint, a part of G.I. Holding. This partnership significantly expands Cooltherm's...